Chlorine Disinfection for Dam Water
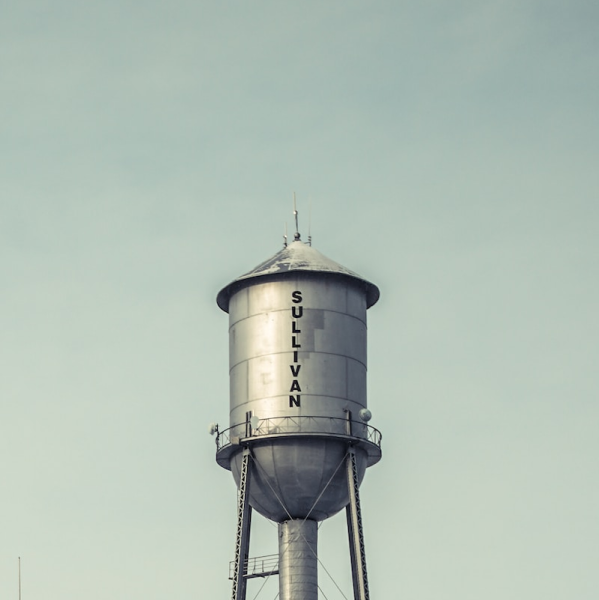
Rainwater and Tank Water
Chlorine acts as three things in an aqueous solution.
Chlorine acts as three things in an aqueous solutio1). We can use a very high strength of chlorine as a poison to remove thick bio-film build up in plumbing with some measure of success.
2). There are times that it method is not suitable is when the chlorine will not release due to low or high pH levels, unless you can adjust the pH.
3). It normally attains lower residual levels of <3ppm as a disinfectant.
4). It can be used as an oxidiser from low to very high doses (up to 30 litres an hour, or more) to remove high levels of bacteria (slug dosing) organics, including organic colour or iron and manganese and remove or extinguish hydrogen sulphide gas.n.
- A poison
- A disinfectant (as used by water authorities)
- An oxidiser
Automatic Chlorine Dosing
Dosing sodium hypochlorite by dosing pump is the only accurately successful method of applying chlorine or you are at risk of overdosing or under-dosing, failing to disinfect, or poisoning users. This is best achieved by pH probe and ORP dosing controller
Dosing can also be achieved by manual dosing pump at a set level, by using a pulse head water meter sending a signal to activate the chemical pump according to flow rates with post testing for free chlorine residual by test kit or using an ORP meter measuring in milli-volts. The residual of free chlorine sought at the most distance end point should be no higher than .2 -.3ppm provided the chemical has removed or eliminated the problem(s).
Manual Set Dosing
Varying Levels
It is possible that the injection of chlorine may need to be quite high at the start point to be effective, or be changed depending on seasonal demands. The residual means that there is still active chlorine available to disinfect or eliminate with the organics or problem sought to be eliminated from the supply water, or needed down-line from the point of injection.
This comprises a computer chip operated chemical doing pump and probe. It is quite easy to set the highest and lowest set points in ORP to the level needed, then increase or decrease the percentage dose rate and set it proportionally so that overdosing does not occur. This is critical when care must be taken not to cause harm downline.
Automatic Dosing
When Demand is High
Problems in water supply that require high levels of chlorine are very high levels of bacteria, heavy iron problems, and high levels of hydrogen sulphide gas. The demand on chlorine can be quite high and you may not deal with all existing problems at once. It is quite common to have to deal with hydrogen sulphide gas first to get the ORP high enough to create that level of oxidant atmosphere to allow soluble iron the form a solid. It is likely that the microbiological contamination will then only be dealt with if enough chlorine residual is left.
All water treatments have a limited contact time. If the water is pumped into a break tank or proper treatment tank, then contact time may be quite sufficient in the tank.
In a pipeline the water flow may need to travel some distance to achieve the same results. It always pays to test close to the injection point then further down the plumbing and points of use to observe results.
Contact Time
Air Support
Air or additional oxygen can be introduced to assist chlorine in water, by aeration of compressed air methods into a pipeline where composite problems exist in a water supply such as iron and hydrogen sulphide gas.
Air is often essential in a tank treatment process using chlorine initially. It will improve the performance and distribution, then help break down the chlorine when the job is done, particularly rainwater tank disinfection.
Aeration alone in a tank, or in a dam or contained body of water is extremely efficient in dealing with a wide variety of problems. This is dealt with under aeration information sheets.
High iron levels, colloidal activity in water, heavy algae infestations or when chlorine is simply not desired. Chlorine will either not penetrate or simply be burnt out before the task is completed. This becomes a job for either high performance flocculants and they will prove to be extremely efficient, or move to Ozone generation.
When Chlorine is Not Suitable
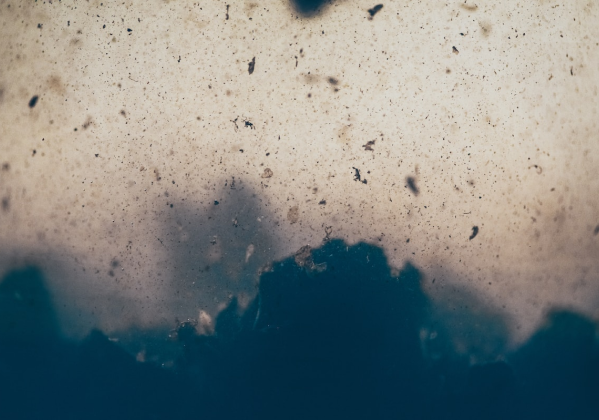
Bacterium
Esherica Coli (E Coli) should not be detected in 100ml of water of drinking water and if detected immediate action should be taken. Salmonela grows out of E high Coli levels Legionella is a risk factor from warm water systems where mist spray is apparent and can come from E Coli but mores so the bacterium following. Legionella can cause Legionnaires disease.
The effect of bacteria contaminated water consumed by persons will show as stomach aches, ear aches and lethargy in that person.

Ultra Violet
In the simplest terms this method produces intense ultra violet waves of light that are contained in a chamber with water flowing around. The water supply needs to be extremely clean for this to be effective as it will not pass through sediment or colour particles but will simply bounce off and the kill or disinfection effect is lost.
Effective filtration prior is critical. Ultra Violet carries no residual ability outside the chamber. It is quite passive in operation.
The plumbing down-line must be disinfected after installation. This is usually performed by a potable chemical that leaves no residue.
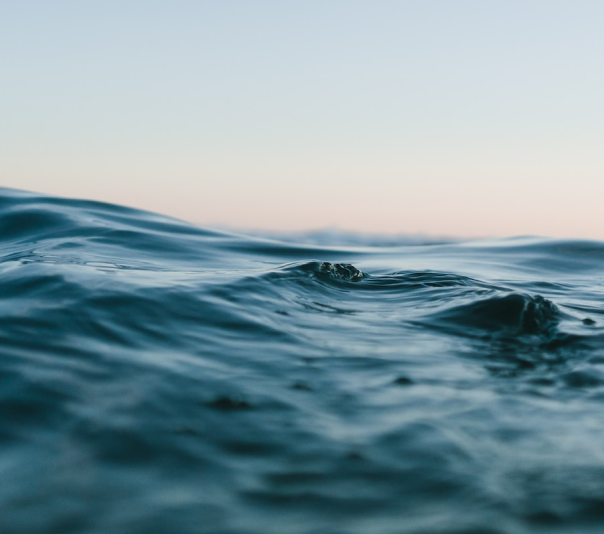
Summary of The Plant
This plant is set up carefully to suit and meet the production needs of each person or water user bringing poor quality bore water up to the standard of each need. These machines are built to last for many years along with the membranes.
We seek to make this process producing the quality of water sought as simple and as automatic as possible. We do the hard work for you.
Analysys
The Aquarius Desalination units design starts with a very comprehensive analysis report so that nothing is missed that could be a problem in the process. We test for 59 items. If iron and or manganese are detected, then it must be removed prior to the filters that come with the plant or they simply foul.
Aquarius Desalination Plant
Installation and Commissioning of Ultra Violet
Once the system is installed proper commissioning is achieved by using a biocide to strip all possible bacteria from places even within the U V chamber down to every last point of use in all plumbing.
The intervals for UV lamp replacement and cleaning should not exceed 12 months. There are uses where the service life is so critical that require service to be more often.
Maintenance includes, stripping the system, cleaning, changing O rings as required then installing the new lamp and re-starting.